- 10 hours ago
- 1 min read
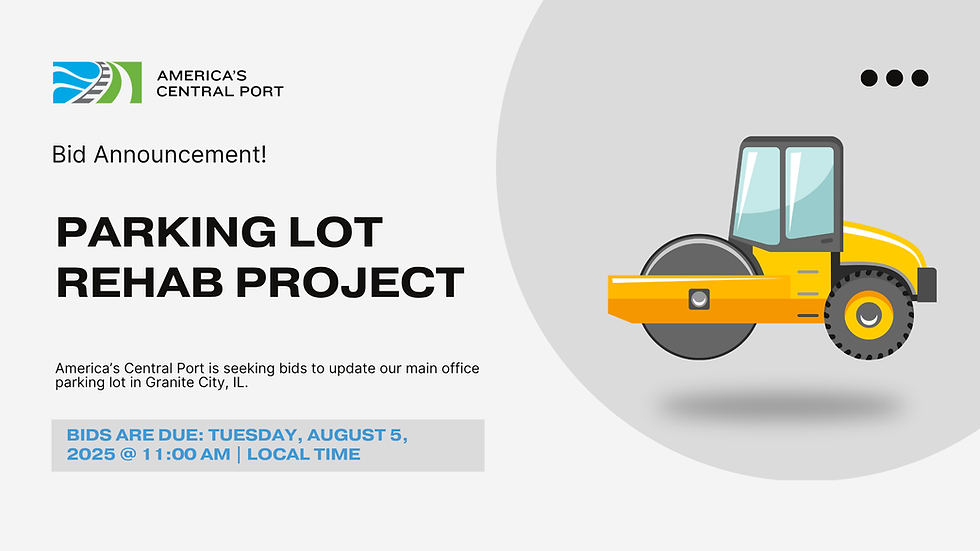
Bid Name: P24-LAND-04 (Building 100 Parking Lot Rehabilitation)
Bids Due: Tuesday, August 5, 2025 | 11:00 AM Local Time @ America's Central Port, 1635 West First Street, Granite City, IL 62040
Project Scope:
This project will resurface the existing parking lot while preparing the site for future phases.
Bid Packet Document:
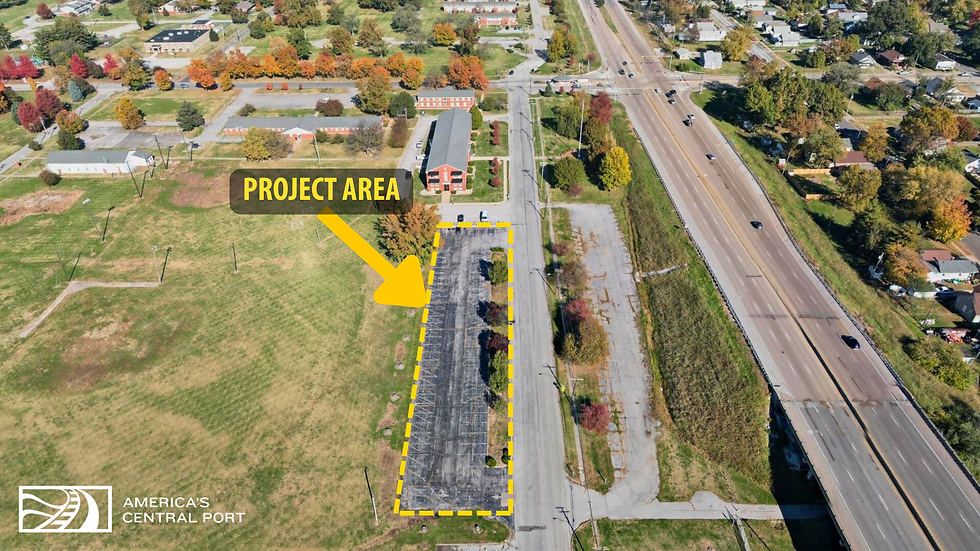
For more information, contact:
Christie Voelker, Director of Planning
(618) 452-8445
To be notified about future bid opportunities, register on our Planroom page here: